
DROPPED OBJECT PREVENTION
The Definitive Guide to Dropped Object Prevention.
This is the ultimate guide to stopping dropped objects when working at height.
First, we’ll learn how tools at height present a constant danger and why dropped tool prevention is more important in the workplace today than ever.
Then, we’ll help you get a safety plan to stop the drops before they even happen.
We can’t just accept that drops are an inherent hazard at work. Instead, we’ll proactively look at how tool lanyards are a practical way to manage these risks.
Sound good? Let’s dive right in…
Contents
- Dropped object definition
- International dropped object statistics
- Reveal the real cost of drops
- Case study: A dropped object fatality
- Understand what causes drops
- Learn about the physics of falling objects
- Discover the methods of containment
- How to train your team
- Get your own dropped object prevention plan
Look:
It’s easy for Health and Safety professionals to think dropped objects and falling tools are a problem too difficult to tackle head-on.
Often they’ll just put a sign up like this
But we know that’s not good enough for you. That’s why you’re here.
So, how should you prevent dropped objects?
By the end of this guide, you’ll have the know-how to get to grips with these hazards at height and introduce your own drop prevention program.
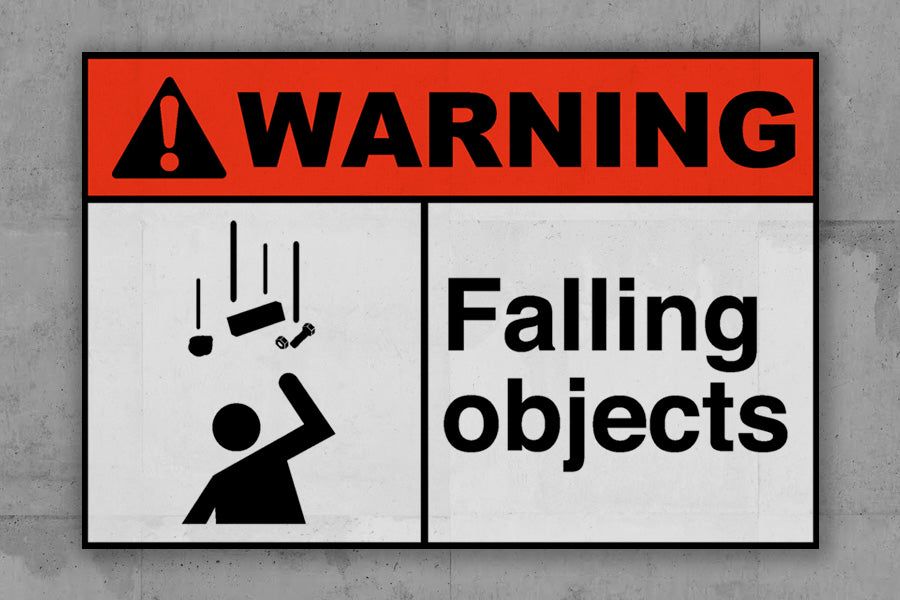
What is a dropped object?
There are the two types of falling objects:
Static Dropped Object
Any object that falls from its previous position under its own weight (gravity) without any applied force. For example, failure caused by corrosion or vibration.
Dynamic Dropped Object
Any object that falls from its previous position due to an applied force. For example, collisions involving moving equipment or loads, snagging on machinery or stacked items, dislodged tools or equipment.
"On average, nearly 140 people are ‘Struck By A Falling Object’ every day in the US."
OSHA
Dropped object statistics
Now it’s time to uncover the staggering dropped object incident statistics from around the world.
United States
In the U.S. in 2016, there were 255 fatalities caused by a falling object.
Source: U.S. Bureau of Labor Statistics 2016
On construction sites alone, there are an estimated 50,000 ‘struck by a falling object’ incidents every year.
Source: OSHA
United Kingdom
The latest statistics from HSE’s Riddor Report 2017/18 show that dropped objects still rank in the top 3 of the UK’s workplace killers.
Falling objects also accounted for over 7,000 reported non-fatal injuries, with 75% of them resulting in over 7 days of lost work time each (2016/17).
Source: HSE’s Riddor Report
Australia
Between 2010 and 2014 falling objects in Australia caused:
- 125 fatalities (that’s more than ‘falls from height’ for the same period!)
- 15,410 Serious Workers Compensations Claims (A serious claim is an accepted workers’ compensation claim that involves one or more weeks away from work).
Source: Safe Work Australia Traumatic Injury Fatalities, 2014
Source: National Data Set for Compensation-based Statistics, Safe Work Australia
Summary
- Even in developed economies, dropped objects are still one of the top causes of fatality.
- With the probability of an incident so high, why has the danger been overlooked for so long?
- Today, no one deserves to be exposed to the risk of falling tools at work.
"Almost every 30 minutes, there is a serious ‘Drop Incident’ in Australia."
Safework Australia
The real cost of drops in the workplace
The costs of dropped objects can be divided into 3 main categories:
Time
Dropping tools and equipment has a huge negative impact on productivity. Often tools fall long distances, requiring considerable time to retrieve. If they fall into water, machinery or other ‘non-retrievable’ locations, it can delay or even prevent the task being completed on schedule.
Money
Dropping and losing tools costs money in terms of damage and replacement. The cost of retrieval in foreign material exclusion (FME) areas, like nuclear plants, can run into millions of dollars. Another important consideration is that, in the event of a dropped object incident, there can be lengthy legal implications and expensive bills to pay. If members of the public are involved, it can compound the problem and lead to other intangible costs, like brand and reputational damage.
Lives
Most importantly, of course, is the potential loss of life. Even with recoverable injuries, it is traumatic for the persons and families involved – it can lead to the loss of income and ongoing medical expenses. Remember, if you are working in public areas, it is not just your workforce at risk, but anyone passing nearby.
Any time an employee dies at work, it is a tragedy with high emotional and financial consequences.
So, how much could just 1 dropped object incident cost you?
According to the National Safety Council, 1 employee death costs 1.4 Million US Dollars (Source: National Safety Council, Injury Facts, 2015 Edition). This includes the direct and indirect costs such as lawsuits, insurance and medical expenses, communications and public relations cost, government and industry fines, and the cost incurred by the time lost on a suspended project.
Don’t forget:
The cost of a workplace fatality extends far beyond the measurement of money.
The death of a colleague will have a deep emotional impact on the workforce. It can lead to numerous concerns, both internal and external to the company. Workers involved in the accident or employees who worked closely with the deceased co-worker can be affected psychologically. All of this impacts on team morale and productivity.
In reality, the true cost of every workplace fatality is incalculable.
Summary
There are 2 types of costs, direct and indirect. Direct costs include legal and medical expenses, whereas reputational damage and lost time are examples of indirect costs.
Is the uncertainty of unlimited incident costs worth the risk?
Tool tethering is like an insurance policy – for less than the cost of an incident, you can stop drops forever.
Case Study: Dropped Tape Measure Causes Fatality
A construction worker in New Jersey was working on a high-rise apartment complex some 400 feet above the ground when he dropped his tape measure.
It plummeted over 50 floors before ricocheting off a piece of equipment.
And then…
It struck a delivery driver on the side of the head, knocking him unconscious. He was taken to Jersey City Medical Center, where he died shortly afterwards.
Expert Tip: Whilst it is observed that the delivery driver should have been wearing a helmet, due to the nature of the side impact of the dropped tool, it is no guarantee that the hard hat would have saved his life.
This incident helps to illustrate the direct and indirect costs caused by one dropped tool accident. Despite the fact that this residential and hotel complex was a crucial project in Jersey’s City’s revitalisation campaign, a small hand tool caused irreparable damage and led to the suspension of one of the largest development projects in Jersey City’s history.
One dropped tool accident cost a man his life – and irreversible loss to his family and community.
At the same time, the suspension of the project cost the main contractor an enormous amount of time and money spent trying to re-calibrate the project following the disaster. Following the accident, the main contractor was forced to contend with insurance costs, public relations, legal issues, and re-allocating and compensating the other contractors working on the suspended project.
Source: New York Times
Summary
A dropped object accident:
Will leave you with irreparable damage – and what you can repair is going to cost a significant amount of money.
Is one way to get media coverage, but probably not the sort your PR team strives for.
The real cost of drops in the workplace
A host of factors can contribute to a dropped object incident.
Statistics show that around 30% of all dropped object incidents are related to design, technical or mechanical issues but almost half can be attributed to human factors.
Almost half of all dropped object incidents can be attributed to human factors
An understanding of the primary causes of the incidents can help conduct more thorough risk assessments by considering these during worksite hazard identification.
Here are the Top 10:
Inadequate Risk Assessment
Failure to identify dropped object hazards
A risk assessment can identify potential energy sources, index tools and equipment required for each task and increase worker awareness about the potential dangers of falling objects.
Human Factors
Operator error, poor behaviour, complacency, neglect
Inadequate training or awareness of hazards, operator error, complacency, neglect and poor reporting can result in compromised safety.
Inadequately Stored or Secured Tools
No tool lanyards or tethers being used. No containment of loose items
Hand tools, power tools, mobile phones, even Personal Protective Equipment (PPE) are all examples of equipment and tools that should be securely tethered with tool lanyards.
Inadequate Procedures
Bad planning, no management of change
As with risk assessments, if the management of change process isn’t in place to identify and control risk from the changes occurring in the workplace, unidentified and new risks may be missed.
Failed Fixtures and Fittings
Corrosion, vibration, poor design, selection or improper installation
Failed fixtures and fittings can and will often dislodge and fall. Regular inspection helps monitor any deterioration so that appropriate measures can be taken.
Poor Housekeeping
Pre-existing hazards from previous tasks
Workplaces and toolkits should be kept organised and tidy. Loose tools and equipment left around pose an unexpected risk to other workers.
Collisions and Snagging
Lifting, travelling equipment, tag lines, service loops
Moving equipment, lifting and tag lines can all cause snagging or collision. The impact of collisions can cause breakage or create other dropped objects and debris.
Inadequate Inspection and Maintenance
Ignoring unsafe conditions
Regular inspections and maintenance repair schedules can help identify corrosion, damages, wear and tear to equipment and structural elements before they become a falling object risk.
Redundant, Neglected and Home-made Tools and Equipment
These should be eliminated
Home-made tools, improvised tool tethers, equipment that is uncertified, or even damaged tools that have been subjected to a previous fall can fail or break unexpectedly. Tools and tool tethering equipment should always be inspected before use.
Environmental Factors
Wind, sea motion, ice, snow, extreme conditions
The effects of these elements are more pronounced in exposed areas, such as working at height on oil rigs, can compromise the stability of equipment, tools and structural features.
Summary
Human factors are responsible for nearly half of all dropped objects.
Stopping drops requires a proactive and informed approach.
Drop prevention training raises team awareness and encourages a collaborative approach.
The physics of falling objects
People often don’t realise the impact forces that are generated when an object is dropped.
Even with some form of protection, the result of being struck by an item of relatively low weight can be significant.
Here’s an example:
A 2kg hammer
↓
Dropped 5M
↓
Will have an impact force of over 1 Tonne.
That’s like an elephant!
Dropped Object Calculator
This calculator helps measure the potential consequences of a falling object and is a very useful tool during the risk assessment process.
Here are a few considerations to bear in mind:
With light objects (<0.1 kg) a key influencing factor is the effect of an object puncturing the skin and damaging tissue/internal organs. The calculator assumes a blunt object, so is not compatible with broken glass, metal shards etc.
The wearing of standard PPE, eg hard hat, safety boots and eye protection, is assumed in the calculator.
Do not subtract the height of an individual. Measure the complete fall distance to the ground.
This dropped object calculator tool is a guide only, providing a cursory indication of the possible outcome.
Source: DROPS
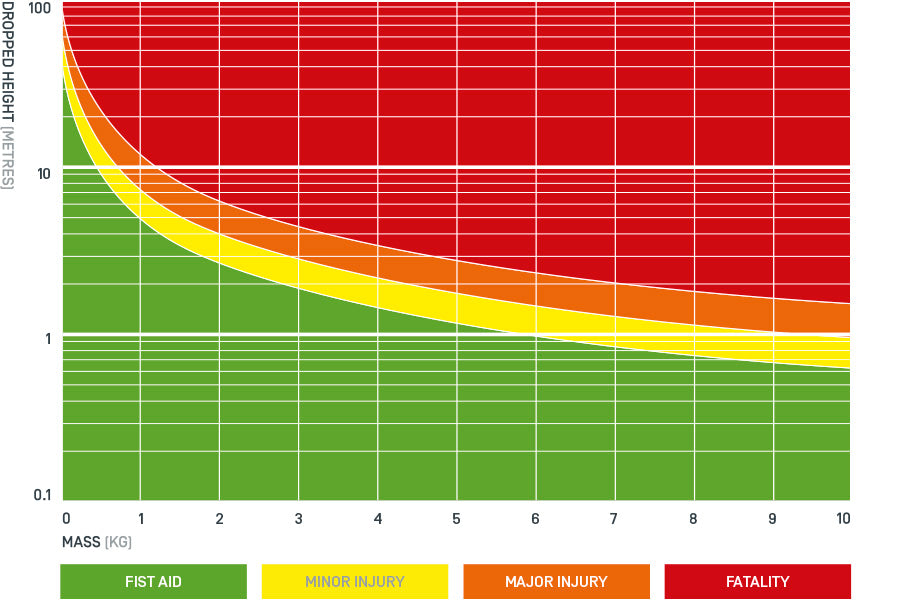
Deflections
There are 2 primary types of incidents:
- Direct impact
- Deflection
Gravity as a force does all it can to make dropped items fall vertically.
But, life isn’t always straightforward. Dropped objects often have their vertical path obstructed, causing the tool to be deflected.
This turns the dropped object into a projectile.
-
You can see the effects of this in the NLG dropped object safety explainer video.
An object that has fallen just 37m (100ft), hitting an obstruction at 6m (20ft), can be deflected over 66m (218ft) away – travelling up to 60mph!
To learn more about deflections, download your Dropped Object Handbook.
Summary
Dropped objects quickly build up a significant impact force – and remember, if they strike a person they don’t always just bounce off, they can penetrate soft tissue with disastrous consequences.
A safe exclusion zone, that allows enough range for deflections, is rarely practical.
With tool lanyards, dropped tools can be safely caught before any impact.
Methods of containment
There are many ways to prevent or reduce the risk of objects falling.
These include toe boards, handrails, netting and hard hats – these examples are all considered to be secondary defence (sometimes called mitigating controls). They are really a ‘back up’ system for when an object has been dropped and are designed to catch it or reduce the impact after the drop.
Tool tethering is a primary system (or preventative control) as it is designed to stop the drop in the first place. Today, proactive Health and Safety Officers across the globe are adopting this methodology and introducing tool tethering policies to stop drops before they happen.
Tool tethering is a preventative control as it stops tools from falling in the first place
Here are some examples of how to stop dropped objects:
Toeboards / Handrails
Kickboards and handrails should be fixed on scaffolding, platforms and walkways. By using additional closed mesh solutions, plywoods or other solid surface materials, coverage can be provided for all the gaps through which items can potentially fall.
Netting
Utilise safety mesh or rated barrier netting (with debris lining) in areas outside walkways and underneath conveyors, walkways, platforms and along building/structure perimeters to prevent the drop of materials to a lower level.
Working Platforms
When possible, lower the working platform to the ground. Perform all work on a structure at ground level and then lift it into position once complete rather than taking the tools and equipment to height.
Tool Tethering System (Primary / Preventative Control)
Utilise tool lanyards, tool tethers, tool pouches, tethering devices, holsters, tool buckets and other drop containment devices to secure tools and other equipment during work at height activities.
Training
Provide worker education on the risks and outcomes of dropped objects and provide them with the means by which they can minimise that risk.
Summary
Mitigating controls can help contribute to a broader dropped object prevention program.
Preventative controls, like tool lanyards, will always be the most effective way to reduce incidents.
Stay a step ahead by proactively managing risk out. Use the Hierarchy of Controls diagram in the handbook to help.
Dropped Object Prevention Training
A great way to start raising awareness is with videos.
Take this dropped objects safety video, for example, Killer on the Loose.
A powerful way to kick things off, isn’t it?
Try using this, or one of these other height safety videos, at your next safety meeting to start a discussion about dropped tools and objects.
You should also consider:
Toolbox Talks
A dropped objects toolbox talk can help launch a program or refocus workers’ attention on tool safety and drop management.
With NLG, you can quickly get access to dropped object prevention PowerPoint presentations (ppt), along with posters and other quick-start guides.
Training
Whether it’s classroom style or online, here are some typical course objectives:
Understand and define what is a potential dropped object.
Know how to identify a potential dropped object and the common causes.
Review methods for the control and prevention of potential dropped objects.
Understand roles and responsibilities in respect of potential dropped objects.
Consider options for maintaining awareness and continuous improvement in the fight against gravity.
NLG Safety Academy
Having your team onboard is crucial to a successful program.
Don’t leave it to chance.
NLG will support you with a structured plan so you can train and test your team’s understanding at every level.
By building on the best practices of Dropped Object Prevention Scheme (DROPS) and collaborating with other industry leaders, NLG has established one of the most trusted dropped object prevention training programmes.
With NLG’s simple training, you can grow your team’s understanding and award them with Approved Safety Academy certificates for successfully completing each course.
Now you can be confident that everyone is onboard and competent.
Summary
If training is conducted in the correct manner, it will streamline the entire implementation process.
Your workforce is worthy of the investment and will give their support for the project when the risks and objectives are clearly understood.
Contribute to your team’s professional development and build a strong culture around drop prevention.
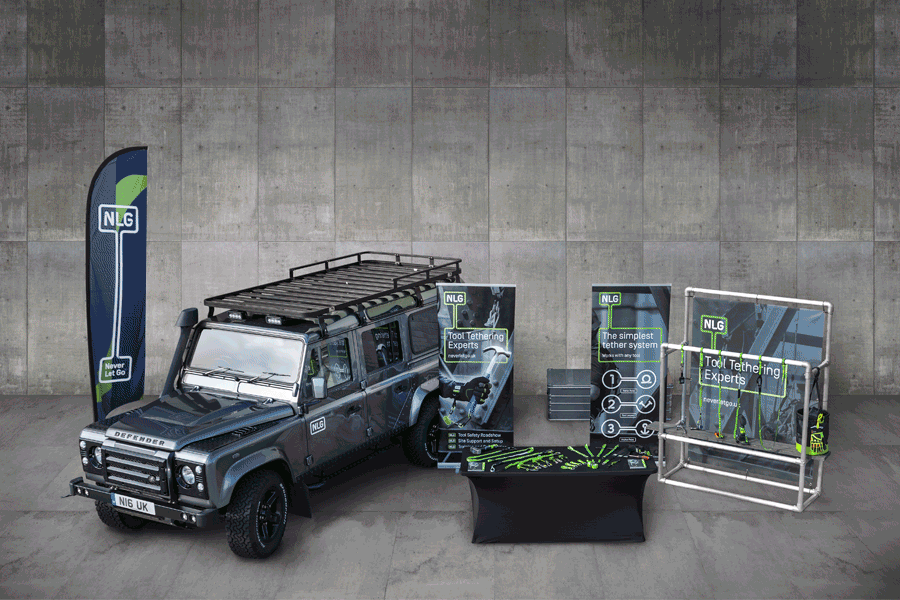
Dropped object prevention plan
The challenges of implementing a tool drop prevention policy can be daunting.
Right?
Understanding your legal requirements, digging into the facts and figures in your industry, presenting the case to the board, detailing your tool inventory, trying to find the right solution, rolling out a training program, not to mention handling negative feedback from disillusioned users.
You’re not alone.
In fact, we find a common thread of challenges that face Health & Safety leaders today.
Here are 5 of the most common concerns:
Awareness
So many workers have been consistently exposed the risk of falling objects. This can lead to some inertia and give way to an attitude of complacency whilst ignoring the management of objects at heights.
Culture
Whilst PPE generally can be interpreted as protecting ourselves, tool drop prevention requires a different perspective. It’s really about protecting our co-workers. Changing perspectives and getting support for a new initiative could be stressful.
Productivity
It is frequently considered that tethering tools would lead to restricted tool functionality and therefore lower output. In turn, workers would be frustrated and job satisfaction decrease.
Expert Tip: This is really a warning against the adoption of poorly designed drop prevention devices as tool tethering should never inhibit the correct use of the tool.
Variety
How can one tool tethering system compass the vast range of tools used by different trades at height on my site? If there isn’t an answer to every question (or an option for bespoke products to my exact requirements), how will the project be sustainable?
Management
Enforcement of a consistent tool lanyard standard could be difficult, particularly when subcontractors are involved. Once implemented, there could be additional responsibilities and pressure on the already busy inspection teams.
We understand. It’s easy to feel this way.
At NLG, we’ve helped hundreds of other companies avoid these challenges and guide them through the same process.
Now we’ll reveal how we’ve done it.
NLG 7 Framework™
The NLG 7 Framework™ is a simple step-by-step plan that maps out everything you need to do on your journey towards your Zero Drop Zone™.
It’s a checklist used by the world’s most progressive organisations to deliver successful dropped object prevention policies, every time.
It will work for you too.
Stop drops, in 7 steps:
Discovery Workshop
Site Awareness
Trial
Policy Template
Training
Site Setup
Spread the word
If you’re committed to stopping drops, you should use it too.
Conclusion
Dropped object prevention is not just an industry trend. It’s a best practice employed by proactive and aspiration safety leaders across the globe.
After all:
One drop can end a life, ruin a family, finish a business.
Organizations that are forward-looking and embrace the movement will be rewarded with more time, more profits, and a happier, healthier workforce.
Yes, it’s really that powerful.
One drop can end a life, ruin a family, finish a business
It used to be difficult to stop drops. But now it’s not.
Get started today.